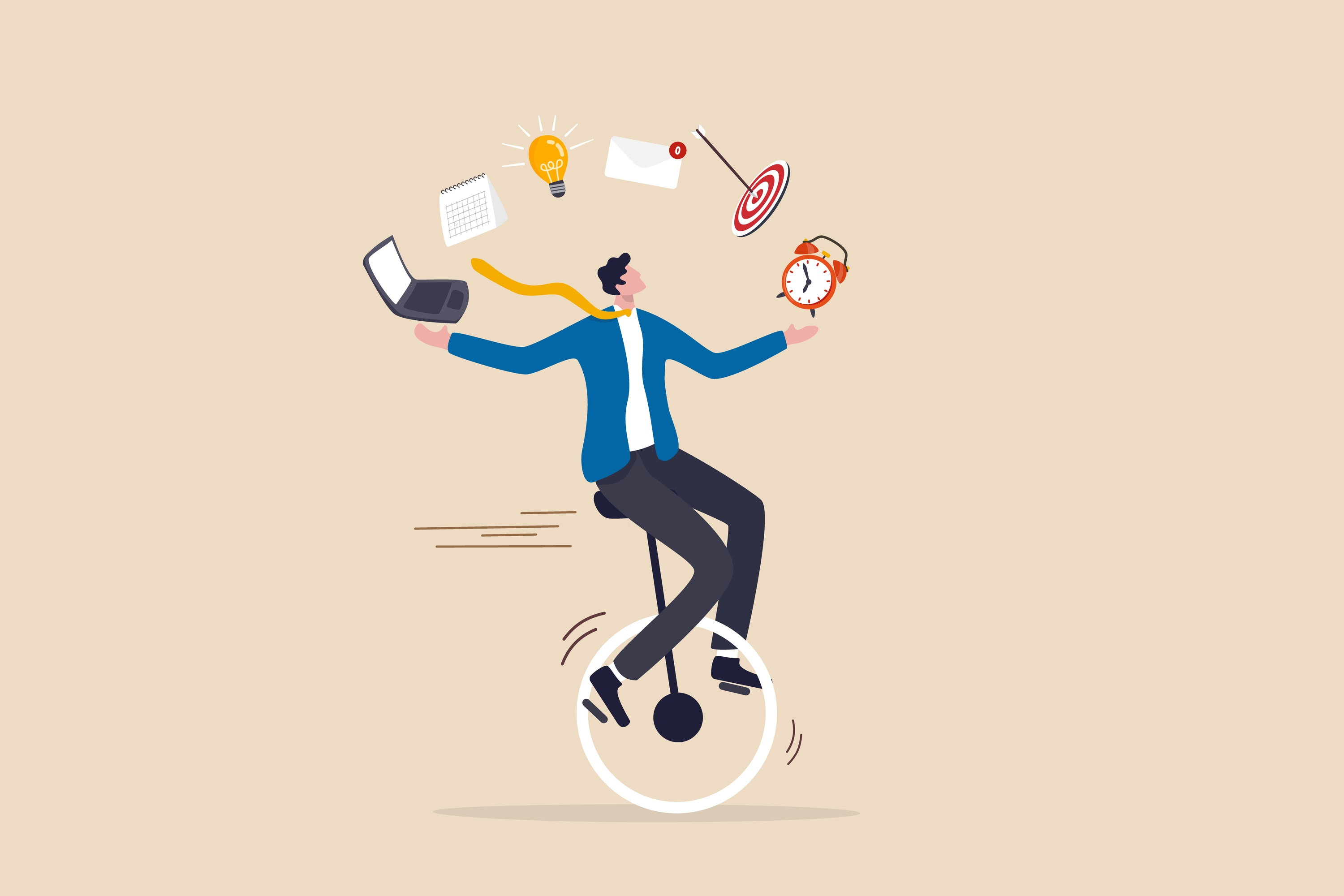
Allungare la vita degli impianti produttivi
Efficienza materica: seconda vita della materia, recupero dei componenti delle macchine e manifattura additiva. Gli esempi di CEPI SPA, DALBELLO SRL, RIVI MAGNETICS SRL E 3DNEXTECH.
La decarbonizzazione del comparto meccanico è fortemente legata al consumo energetico, partendo dalla produzione della materia prima fino al possibile riciclo a fine vita. L’industria meccanica è storicamente legata al riutilizzo della materia prima, dal momento che tutti i metalli possono essere riciclati con ottimi risultati anche in termini di recupero energetico ed ambientale, perché produrre un metallo puro dal minerale è un ciclo di produzione altamente più impattante. La transizione green del settore passa però anche per quelle azioni volte ad allungare il ciclo di vita di un prodotto. Troppo spesso l’innovazione tecnologica si concentra sui concetti di miglioramento o efficientamento di performance, quale ad esempio i consumi in fase di produzione oppure il rendimento in fase di recupero o riciclo. La transizione digitale può invece trovare un enorme potenziale di applicazione green in una logica di allungamento del ciclo di vita di un impianto produttivo attraverso il retrofitting o il revamping, nella convinzione che il miglior modo di fare industria “sostenibile” sia limitare gli sprechi e riutilizzare ciò che è già stato usato.
Un esempio virtuoso in questo senso ci viene proposto da CEPI SPA, azienda che progetta, costruisce e installa impianti chiavi in mano per lo stoccaggio, trasporto e dosaggio di materie prime, operando prevalentemente, ma non esclusivamente, nel settore alimentare. Sin dalle sue origini, CEPI ha messo al centro ricerca e adattabilità, puntando a costruire impianti chiavi in mano completamente automatizzati in grado di gestire l’intera linea di produzione dallo stoccaggio al dosaggio, e a sviluppare soluzioni altamente specializzate per venire incontro ai bisogni più disparati di materie prime e processo. Manifattura diretta di tutte le attrezzature e completa integrazione verticale, assicurano la massima efficienza e diversificazione, garantendo continuità delle operazioni e supporto su tutti i fronti. Per quanto concerne la circolarità nell’ambito dei processi produttivi, CEPI lavora l’acciaio inox, materiale altamente riciclabile. Inoltre, questione molto rilevante, l’azienda progetta da sempre i suoi impianti in modo che siano facilmente riparabili e modificabili negli anni. Le attività di revamping presso i clienti sono frequenti: ne deriva un ciclo di vita lunghissimo, che porta ad avere la gran parte degli impianti costruiti nei vari decenni ancora in funzione. Tutto ciò è reso possibile dalla grande attenzione che l’azienda pone alla fase di ideazione di ogni nuovo impianto che viene disegnato per ottimizzare i consumi energetici ed è equipaggiato con motori ad alta efficienza per risparmiare energia e ridurre le emissioni, ma soprattutto progettato tenendo conto dei potenziali sviluppi futuri, consentendo la massima flessibilità e un facile revamping.
Efficienza materica: seconda vita della materia, recupero dei componenti delle macchine e manifattura additiva
Recuperare materia e valorizzare scarti per dar loro una seconda utilità è tra i pilastri dell’economia circolare, e la meccanica negli anni sta dando una mano all’industria sviluppando impianti adatti a questa sfida.
DALBELLO SRL, uno dei brand italiani più famosi al mondo nella produzione di scarponi da sci, lavora da un paio d’anni al progetto REPAIR 3D1, finanziato dall’UE all’interno del programma Horizon 2020. Il progetto è dedicato alla ricerca di nuove metodologie per il riciclo e il riutilizzo di rifiuti plastici e di materiali compositi contenenti fibra di carbonio per la produzione di scarponi da sci innovativi, i cui componenti saranno realizzati attraverso processi di stampa 3D. Gli scarponi prodotti conterranno fino al 70% di materiali riciclati, provenienti da diverse fonti, dalle aziende aerospaziali a quelle dell’industria automobilistica, ma soprattutto saranno facilmente disassemblabili, in modo da poter separare più efficacemente i singoli componenti e poterli riavviare verso un ulteriore processo di riciclo. Il design by product di questa innovativa generazione di scarponi da sci, la costruzione di un impianto pilota di separazione dei componenti e dei materiali e la definizione di un nuovo modello di business circolare sono invece alla base del progetto LIFE RESKIBOOT11, finanziato dalla Commissione Europea e partecipato dalla stessa DALBELLO SRL insieme a RENT a Sport Italia Srl, Studio Fieschi & Soci Srl e Plastic Sort Srl.
Una risposta tanto semplice quanto concreta alla minor impronta carbonica di prodotto sta anche nella capacità di poter riutilizzare alcuni componenti, allungandone così il ciclo di vita.
RIVI Magnetics Srl, azienda fondata nel 1968 come azienda di manutenzione delle macchine per la ceramica, dal 1971 produce sistemi di ancoraggio magnetico, che vengono utilizzati dall’industria per lo stampaggio della gomma, dal settore delle macchine utensili, dal metal stamping per la lavorazione della lamiera fino all’industria per lo stampaggio della plastica. L’azienda attua da sempre una decisa politica di investimenti in ricerca e sviluppo, formazione e adeguamento tecnologico agli standard richiesti dalla quarta rivoluzione industriale, ma sta ovviamente cercando di implementare soluzioni anche nell’ambito della transizione green. L’idea a cui sta lavorando l’azienda consiste nella messa a punto di un servizio di ritiro dei piani magnetici usati12 per recuperare i piani magnetici a fine vita e riutilizzarne i principali componenti in produzione. Ciò permetterebbe di aumentare il quantitativo di materiali riciclati all’interno dei nuovi prodotti o addirittura di praticare il riuso di alcuni componenti, con risparmio sull’acquisto di materie prime e la diminuzione dell’utilizzo di terre rare, notoriamente poco sostenibili. Tale servizio, comunicato già al momento della vendita e comunicato a tutti i clienti in essere, può essere organizzato in riferimento a metodologie riferite al C2C (Cradle to Cradle)2 applicando tecniche specifiche di ecodesign.
3DNextech è una startup innovativa, spin-off dell’Istituto superiore Sant’Anna di Pisa, che studia e realizza soluzioni per l’efficientamento della filiera della manifattura additiva. La startup ha sviluppato un processo di lavorazione della plastica che agisce a livello molecolare rendendo i polimeri malleabili senza l’utilizzo di calore. Un sistema che ha la capacità di rendere particolarmente vantaggiosa, in molti contesti, la produzione di oggetti tramite manifattura additiva.
Applicata alle fasi successive alla produzione, la tecnologia attribuisce agli oggetti stampati proprietà meccaniche indispensabili, altrimenti difficilmente conseguibili. Applicata alla fase di produzione – e quindi di stampa- rende possibile creare componenti su misura quando e dove serve, senza sprechi di materiale, senza produzioni di massa per l’abbassamento dei costi e senza spostamenti di merci da una parte all’altra del mondo.
In prospettiva, questa tecnologia è dunque in grado di eliminare l’utilizzo di energia termica, di utilizzare rifiuti plastici come materia prima, e di accelerare i tempi di produzione, abilitando un accorciamento drastico delle catene logistiche.
– Tratto dal rapporto annuale “GreenItaly 2022” di Symbola e Unioncamere –
Note:
- Stime The European Hou- se-Ambrosetti e Snam.
- https://repair3d.net/
Autore
-
Relationship Manager di Warrant Hub – Tinexta Group e coordinatore del progetto Warrant GARDEN (Green Advanced technology Research and Development Economy), che si occupa della consulenza e dell’orientamento in tema di sostenibilità per le imprese. Laureato in Economia e Gestione delle imprese, dopo un’esperienza in ambito bancario, è entrato in Warrant Hub nel 2003, occupandosi dapprima di Business Development, per poi passare allo sviluppo di partenariati e di relazioni con le istituzioni europee nell’ambito di progetti e programmi UE per la ricerca e l'innovazione. Promotore della Digigreen Innovation e autore di diversi articoli sul tema della transizione digitale e verde, è docente dell’Online Certification Program for Digigreen Professionals del MIP Politecnico di Milano e del Master Executive SUSTMAG di Unitelma Sapienza. Da gennaio 2021 è membro del comitato tecnico scientifico di MADE – Competence Center Industria 4.0.
You may also like
RIFIUTI INDUSTRIALI, L’ITALIA PERDE 1 MILIARDO L’ANNO
Occorre, secondo Asso Ambiente, "un quadro normativo rigoroso, ma inequivocabilmente applicabile, ch
Giornata Mondiale delle Api e della Biodiversità: Promuoviamo una Transizione Eco-Sostenibile
Ascolta il Podcast La Giornata Mondiale delle Api e della Biodiversità, celebrata il 20 maggio di o
L’impatto della Lieferkettengesetz sulle Catene di Fornitura Italiane
Ascolta il Podcast 🎧 La Lieferkettensorgfallspflichtengesetz (LkSG), o Legge sulla Catena di Forn